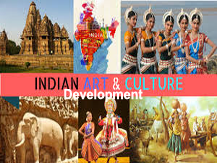
Mera Bharath Mahan is committed towards the revival of Culturals/Traditional art and craft development.
.Our Services are :
- Help to Develop our Indian Culture
- Help to Develop our Traditions
- Help to Develop Traditional art and craft
OUR STATES

The India Cements Ltd was established in 1946 and the first plant was setup at Sankarnagar in Tamilnadu in 1949 . Since then it has grown in stature to seven plants spread over Tamilnadu and Andhra Pradesh . The capacities as on March 2002 have increased multifold to 9 million tons per annum.
The Company is the largest producer of cement in South India.
• The Company's plants are well spread with three in Tamilnadu and four in Andhra Pradesh which cater to all major markets in South India and Maharashtra.
• The Company is the market leader with a market share of 28% in the South. It aims to achieve a 35% market share in the near future.
• The Company has access to huge limestone resources and plans to expand capacity by de-bottlenecking and optimisation of existing plants as well as by acquisitions.
• The Company has a strong distribution network with over 10,000 stockists of whom 25% are dedicated.
• The Company has well established brands- Sankar Super Power, Coromandel Super Power and Raasi Super Power.
• Regional offices in all southern states and Maharasthra offices/representative in every district.
53 Grade Cement - Coromandel King-Sankar Sakthi- Raasi Gold
Coromandel King, Sankar Sakthi and Raasi Gold are high strength cements to meet the needs of the consumer for high strength concrete. As per BIS requirements the minimum 28 days compressive strength of 53 Grade OPC should not be less than 53 Mpa. For certain specialised works such as prestressed concrete and certain items of precast concrete requiring consistently high strength concrete, the use of 53 Grade OPC is found very useful. 53 Grade OPC produces higher-Grade concrete at very economical cement content. In concrete mix design, for concrete M-20 and above Grades a saving of 8 to 10% of cement may be achieved with the use of above mentioned 53 Grade OPC.
43 Grade Cement - Coromandel-Sankar-Raasi
Coromandel, Sankar and Raasi are the 43 grade OPCs most popular general-purpose cement in the market today. The production of 43 grade OPC is nearly 50% of the total production of cement in the country
The compressive strength of cement at 28 days when tested as per IS code shall be minimum 43 Mpa. Characteristic strength requirements of this cement are given in the chart
BLENDED CEMENT
Coromandel Super Power, Sankar Super Power and Raasi Super Power are the premium blended cements from THE INDIA CEMENTS LIMITED. It is produced by intergrinding of OPC clinker alongwith gypsum and mineral admixtures. Dedicated to the end user after passing through stringent tests at our R&D laboratory, it ensures durable structures that lasts for generations.
Sulphate Resisting Portland Cement (SRC)
Sankar SRC can be used for structural concrete wherever OPC or PPC or Slag Cement is usable under normal conditions.Sankar SRC is particularly beneficial in such conditions where the concrete is exposed to the risk of deterioration due to sulphate attack. For example, in contact with soils and ground waters containing excessive amounts of sulphates as well as for concrete in seawater or exposed directly to seacoast. The IS 456 1978 (revised draft code ) has made elaborate provisions for use of particular type of cement against different percentages of soluble sulphate salts.

UltraTech is India's largest exporter of cement clinker. The company's production facilities are spread across five integrated plants, five grinding units, and three terminals — two in India and one in Sri Lanka. All the plants have ISO 9001 certification, and all but one have ISO 14001 certification.
UltraTech's products include Ordinary Portland cement, Portland Pozzolana cement and Portland blast furnace slag cement.
RDINARY PORTLAND CEMENT
PORTLAND BLAST FURNACE SLAG CEMENT
PORTLAND POZZOLANA CEMENT
Cement to European and Sri Lankan norms
Ordinary Portland cement
Ordinary portland cement is the most commonly used cement for a wide range of applications. These applications cover dry-lean mixes, general-purpose ready-mixes, and even high strength pre-cast and pre-stressed concrete.
Portland blast furnace slag cement
Portland blast-furnace slag cement contains up to 70 per cent of finely ground, granulated blast-furnace slag, a nonmetallic product consisting essentially of silicates and alumino-silicates of calcium. Slag brings with it the advantage of the energy invested in the slag making. Grinding slag for cement replacement takes only 25 per cent of the energy needed to manufacture portland cement. Using slag cement to replace a portion of portland cement in a concrete mixture is a useful method to make concrete better and more consistent. Portland blast-furnace slag cement has a lighter colour, better concrete workability, easier finishability, higher compressive and flexural strength, lower permeability, improved resistance to aggressive chemicals and more consistent plastic and hardened consistency.
Portland Pozzolana cement
Portland pozzolana cement is ordinary portland cement blended with pozzolanic materials (power-station fly ash, burnt clays, ash from burnt plant material or silicious earths), either together or separately. Portland clinker is ground with gypsum and pozzolanic materials which, though they do not have cementing properties in themselves, combine chemically with portland cement in the presence of water to form extra strong cementing material which resists wet cracking, thermal cracking and has a high degree of cohesion and workability in concrete and mortar.

Zuari Cement is part of the Italcementi Group, the fifth largest cement producer in the world and the biggest in the Mediterranean region. With net sales over 6 billion Euros in 2007 and a capacity of 70 million tonnes.
Italcementi Group combines the expertise, know-how and culture of a number of companies from more than 22 countries in 4 continents. This includes an industrial network of 63 cement plants, 15 grinding centres, 5 terminals, 134 aggregates quarries and 613 concrete batching units. In India, with its inherent strengths, Italcementi Group's Zuari Cement is committed to give the building industry a cement that is truly international.
A commitment to customer satisfaction has seen Zuari Cement grow from a modest 0.5 million tonne capacity in 1995 to 3.5 million tonne today. Zuari Cement is in the process of increasing this capacity to 6 million tonne by 2009 through setting up of a new 5500 tonne per day clinker line at Yerraguntla and a grinding center at Chennai. A captive power plant with a capacity of 43 MW has already been set up at the Company's cement manufacturing facility at Sitapuram. With a 6% market share in the south Indian cement market and sales of about Euro 174 million in 2007, Zuari Cement has chalked out ambitious plans for the future. This includes strengthening its presence in the Maharashtra, Orissa and West Bengal markets. While technology is just one of its strengths, there are many other factors that contribute equally to Zuari's success. These include a high-level organisation and decentralised quality assurance teams to guarantee the full compliance with the customers' expectations.
Italcementi Group at a glance
With an annual production capacity of approximately 70 million tons of cement, Italcementi Group is the world’s fifth largest cement producer. The Parent Company, Italcementi S.p.A., is one of Italy’s 10 largest industrial companies and is included in S&P/MIB Index of the Italian Stock Exchange. Italcementi Group’s companies combine the expertise, know how and cultures of 22 countries in 4 Continents boasting an industrial network of63 cement plants, 13 grinding centres, 5 terminals, 125 aggregates quarries and 614 concrete batching units. In 2008 the Group hadsales amounting to almost 6 billion Euro. Italcementi, founded in 1864, achieved important international status with the take-over of Ciments Français in 1992.
Following a period of re-organization and integration that culminates in the adoption of a single corporate identity for all Group subsidiaries, the newly-born Italcementi Group began to diversify geographically through a series of acquisitions in emerging countries such as Bulgaria, Morocco, Kazakhstan, Thailand and India, as well as operating in North America. As part of the plan to further enhance its presence in the Mediterranean area, in 2005 the Group boosted its investments in Egypt becoming the market leader.
In 2006 Italcementi acquired full control of the activities in India and signed an agreement to strengthen its position in Kazakhstan while, in 2007, it further strengthened its presence in Asia and the Middle East through the operations in China, Kuwait, Saudi Arabia. In 2008 the Group signed a joint venture in Libya to build a 4 million tons/year cement plant. As a member of the World Business Council for Sustainable Development(WBCSD) Italcementi Group has signed the Cement Sustainability Initiative’s Agenda for Action, the first formal commitment that binds a number of world cement industry leaders to an action plan that aims at satisfying present-day needs at the same time as safeguarding the requirements of future generations. To further confirm its commitment on these issues, the Group has taken over the co-Chairmanship of the Cement Sustainability Initiative for the period 2006-2007.

Penna Cement Industriies Limited (PCIL) was formed in year 1991 by Mr. P. Prathap Reddy. First plant was commissioned in 1994 at Talaricheruvu village in Tadipatri Mandal of Ananthapur district of Andhra Pradesh with initial capacity of 0.2 mtpa.
Penna Cement Industriies Limited is an ISO 9001:2008 Company.
Penna is well positioned for continued growth and market dominance because of its vibrant leadership. Under the able leadership of founder promoter, Mr.P.Prathap Reddy, the management has taken significant steps to renew and refresh the core business of cement manufacturing for tomorrow, making the company achieve greater heights

Every land mark stands for it. Truly a distinct winner, KCP Cement is Nation’s premier conglomerate and it has a series of advantageous characteristics that makes it the epitome of strength and trust.
>> Superior Strength of Structure
>> Assured Structural Safety
>> Savings out of rational cement consumption
>> Enhanced life of building
>> Better Bonding of structures
>> Cost and time saving through prompt construction
>> Long term Economy in Building Maintenance.
Relationships – Mutual benefits In an ever evolving market there are two factors that govern ones success, “Quality and Distribution”, the arenas where people are the players. At KCP our understanding unto it goes deep. Having produced quality products with the dedicated support of every employee, the group extends a devoted and supportive hand to its distribution network. The result – A Golden Investment for every KCP Cement Dealer. Factory fresh KCP Cement is distributed directly to our extensive market outlets all over South India, through our committed transport network.

My Home Industries, Maha Cement and Maha Shakthi are the finest blend of Indian Values and International Standards and World Class Technology. My Home Industries is a joint Venture between My Home Group and CRH Plc, an Irish building material major having presence in 33 countries across 3,500 locations.

This is an Ordinary Portland Cement which surpasses the requirements of IS12269-1987 Grade. It is produced by inter grinding of high grade clinker (with high C3Scontent) and right quality gypsum in predetermined proportions.
This product is recognized for its High early strength and excellent ultimate strength because of its optimum particle size distribution, superior crystalline structure and balanced phase composition and hence widely used and suitable for Speedy construction, Durable concrete and Economic concrete mix designs.
Low percentages of alkalies, chlorides, magnesia and free lime in OPC 53 Grade cement leads to the production of durable concrete.

Chettinad cement is operating its cement business spanning three generations. Since its establishment in 1962 with a wet process cement plant at Puliyur near Karur, Chettinad cement has been expanding and making itself versatile in the field of cement products.
Major supplier of Southern India cement needs, Chettinad Cement supplies the "glue" upon which many residential, commercial and engineering projects are built. Chettinad Cement has established its position in the southern market by innovatively aligning its products and services to the needs of cement users.
Chettinad Cement's modern, flexible manufacturing plant produces a wide range of cements which can be delivered in bulk using reliable road tanker fleet.
Under its Builders Choice brand name, Chettinad Cement offers an extensive range of bagged products that includes Ordinary Portland cements and blended cements to suit most building and construction applications. For over four decades, the Chettinad cement companies have built a reputation for serving the construction industry with high-performance products that encourage creativity and ensure longevity. As the creative use of cementitious materials continues to grow in popularity, in both masonry and concrete applications, so too, does our commitment to providing customers with the widest range of cements to achieve the maximum in creativity, versatility and integrity.
Chettinad Cements are carefully proportioned, highly accurate blends of quality materials including blended cement& Portland cement are manufactured under controlled conditions assuring reliable performance, and providing consistent quality.
Chettinad Cement has always strived for high quality production and maintained international standards. The company has won many laurels for its cement production and has ISO 9001/2008, ISO 14001/2004 and IS 18001/2007 certifications. It has grown steadily from time to time through its consistent quality and customer service.

Founded in 1935 by Jaidayal Dalmia; the cement division of DCBL was established in 1939 and enjoys a heritage of 70 years of expertise and experience. We are headquartered in New Delhi with cement, sugar, travel agency, magnesite, refractory and electronic operations spread across the country.
The Dalmia Group had established four cement plants in pre-independence years, two of which were affected by the partition and Independence. The two remaining plants operate as Dalmia Cement and we have also made strategic investment in Orissa Cements Limited(OCL). Managed by a professional team, we have sustained the path to innovation and growth for seven decades.
Early on in our history we learnt that a strong business is an amalgamation of strong relationships.
The key to establishing such relationships is to learn from each other, to enjoy a spirit of camaraderie, and to recognize and identify with their needs of the people we work with. Today with their rich experience we have been able to broaden our horizons to include a holistic approach to the best practices in the industry.
DCBL prides itself on having been at the forefront of pioneering and introducing many new technologies, which exist today, which are followed by others in the industry. DCBL has been and continues to be an industry leader in the niche market segments.
This timeline highlights some of the significant moments that took place over the years and shows how our business has evolved.
Our Services
- Help to Develop our Culture
- Help to Develop our Traditions
- Help to Develop art and craft